Download a PDF version of this article.
Introduction
Whilst decorative floor finishes are not included under the warranty policy cover, the following good practice guidance is given to developers for the installation of ceramic floor tiling and laminate floor finishes.
Ceramic floor tiling
Where ceramic tile floor finishes are proposed on timber floor joists under normal loading, the timber joists will deflect more than the allowable tolerances that a 'ceramic covering' can accept and cracking in the tiles, particularly at floor board junctions, will occur.
General points
- For walk-in showers and wet rooms, timber floor deck substrate is not acceptable
- Ceramic tiling should:
- Be solidly bedded on an approved flexible adhesive/grout
- Should be slip resistant
- Laid to a level finish
- Tiles should be suitable for laying over a timber base and flexible tile adhesive (e.g. C2S) and grout should be used in accordance with the adhesive manufacturer’s recommendations
- De-coupling layers: These provide an intermediate substrate between the tile covering and load bearing substrate including timber floors. They are designed to neutralise lateral stresses that occur between the substrate and tile covering; they are not designed to accommodate differential vertical movement. De-coupling layers are considered to offer a robust approach to preventing ceramic tile failures, where ceramic tiles are laid on a flexible timber substrate
For new floors
The guidance below relates to ceramic tiling only and does not apply to other heavier tiles such as marble, travertine or stone which would be considered too heavy for a traditional suspended timber floor construction.
The floor should be fit for purpose and have adequate stiffness to support the tiles and adhesive.
For floors supported by joists up to 600mm maximum centres, the floor decking should be:
- 18mm exterior grade plywood screwed to the joists at 300mm centres with all square edges supported on joists or noggins. Plywood should be laid with a 1.5mm-2mm movement gap between boards and at abutments OR,
- Moisture resistant floor decking overlaid with a minimum 10mm exterior grade plywood fixed to joists at 300mm centres OR,
- A combination of one of the above with a proprietary separating/de-coupling layer, tile backer board or tile bedding reinforcement sheet used in accordance with manufacturer's recommendations
In addition, the following should be considered:
- The length of screw fixings should be at least 2.5 times the thickness of the combined decking material to ensure adequate penetration into the timber sub-floor or joist /strut supports.
- Additional solid timber strutting between the joists will be required to assist in stiffening the floor construction for the entire span of the joists between supports, this may include strutting beyond the area of the tiled room e.g. if the joist span continues over a landing area.
For existing floors (e.g. in conversions)
Existing timber floors to be covered by ceramic tiles should be sufficiently strong and rigid, therefore:
- Prove the existing floor construction is able to take the additional dead load of up to 0.8 kN/m2 without excessive deflection. Older properties tend to have smaller depth floor joists than current standards for new joists for the same span! Alternatively replace or strengthen the floor joists, as per a Structural Engineers design.
- Existing floor boards should be either removed, or exposed from underneath, to allow the floor to be stiffened with noggins, as described both above and in the 'new homes' section.
- The existing floor covering or new floor covering, dependent upon how the above point is addressed, must then be treated in accordance with the ‘new floors’ section above
Walk-in showers and wet rooms
For walk-in showers and wet rooms, timber floor deck substrate is not acceptable.
Laminate floor finishes
Careful attention should be made to the following:
Substrate:
- Must be clear of debris prior to the installation of the decorative floor covering
- If the decorative flooring is to be laid over an in situ concrete floor or screeded floor; sufficient time must elapse before the decorative flooring is installed. This is because the concrete / screed needs to dry out sufficiently. A floor which hasn’t dried out sufficiently could damage the finished/affect the fixings. Typically, a 50mm concrete screed could potentially take two months to cure.
- Will a suitable DPM/VCL/slip membrane be necessary to protect the finished flooring?
- Check for potential leaks from badly fitted waste pipes or incorrectly detailed thresholds which could result in dampness under the finish resulting in damage/expansion of the floor finish
- In the case of a concrete screed;
- Is it of sufficient thickness and mix to correctly distribute loads, especially if the screed is over an insulation board?
- Sufficiently level and free from high spots. Note that the floor finish must meet our Tolerances requirements if in place at completion, so the substrate must also be construct to meet the Tolerance requirements
- If sound insulation is required to be installed to meet the building regulation requirement; this should not be tampered with and in the case of floating floor insulation; the manufacturer’s details must be checked for requirements of acceptable finishes above the insulation layer.
- If supporting construction is required, this must be installed to the manufacturer’s recommendations and appropriate for the floor finish
- Timber battens must be preservative treated including any cut ends
- Supports must be fixed and at suitable centres to avoid excessive movement
- Provision for heavy loads e.g. Kitchen units, cookers, washing machine, cast iron baths, boilers or other heavy items should be allowed for in the support construction. The floor finish must also be suitable for such loads and not result in the floor finish locally deflecting.
- Support must not be compromised by waste pipes, plumbing or under floor heating systems
Floor finish product:
- Should be suitably protected from damage and extreme temperatures or/dampness prior to installation
- Should be installed in accordance with the manufacturer’s recommendations. This includes using the recommended fixings appropriate for the substrate.
- Must be appropriate for the environment location (e.g. bathrooms, kitchens with high moisture potential)
- Be laid to a level finish without using excess means of additional thickness of adhesive or packing
- Ensure sufficient movement joints and provision for expansion is allowed for at the perimeters, door openings and around fittings, pipes etc.
- Intermediate expansion joints may be required to large floor or open plan areas. The manufacturer’s recommendations should be followed.
- Be laid to meet the warranty tolerances requirements (see below)
- Allowance for adjustment may be necessary after initial contraction or expansion has occurred
General points:
- If underfloor heating is proposed, the developer must ensure that the chosen floor finish is suitable for use with under floor heating. The flooring manufacturer’s details must be checked to confirm this and, where proven suitable, their installation recommendations carefully followed including guidance to follow when underfloor heating systems are used for the first time (to avoid damage to floor finishes).
- The completed floor finish must be clean and free from surplus adhesive or raised fixings
Warranty tolerance requirements for floors
Floor levels
The effects of normal drying out/shrinkage of floors (timber and concrete) may result in minor differences in level and can result in squeaking of materials as they move against each other which might not be able to be eliminated entirely.
- The floor must be relatively flat. Maximum deviation of +/- 5mm is permissible using a 2m straight edge with equal offsets.
- Floors must be relatively level. Maximum deviation of 3mm per 1m is permissible for floors up 6m in length.
- Floors over 6m horizontal length are permitted to have a maximum deviation of 20mm across their length
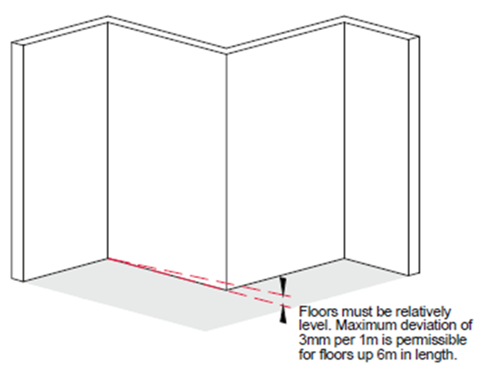
(Reproduced from the February 2023 version of the Technical Manual Section 20 - tolerances)
Floor defection limits
The deflection limit must be 0.003 X the span with a maximum deflection of 14mm where strutting is provided and 12mm where strutting is not provided. This is based on the total and imposed loads for combined bending and shear.
The engineer must ensure that the design of the floor construction does not deflect greater than the above tolerances, unless the relevant BS or EN design code requires the deflection to be smaller.
Read more articles on InSite and sign up to receive our blog round-up.
Every care was taken to ensure the information in this article was correct at the time of publication (June 2023). Guidance provided does not replace the reader’s professional judgement and any construction project should comply with the relevant Building Regulations or applicable technical standards. For the most up to date Premier Guarantee technical guidance please refer to your Risk Management Surveyor and the latest version of the Premier Guarantee Technical Manual.
MK-3563